Shape Optimization of Components
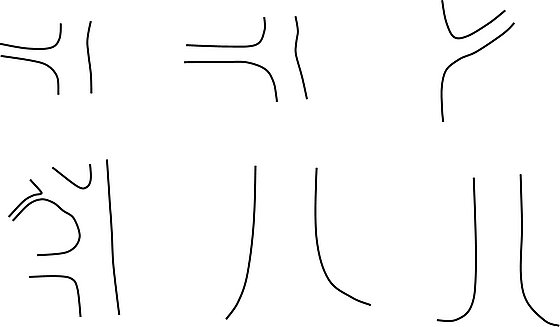
The shape of technical products is often a compromise of aesthetics and mechanical requirements. Aesthetics and mechanics do not necessarily need to compete with each other, which has been proven through many structures found in nature. Those shapes develop themselves based on the applied forces.
Shapes in Nature
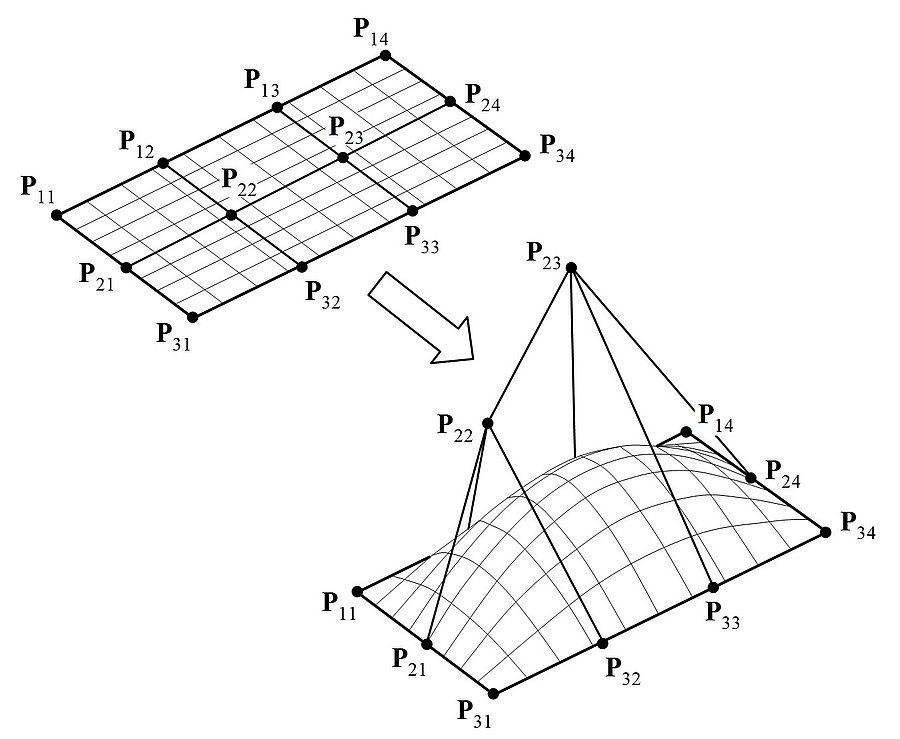
The studies regarding shapes of bones and trees have been very rich. A bone or a tree grows in such a way, that the distribution of stress remains consistent. Moreover, the shapes indicate the history. For example, the wind load to which a tree was exposed to can be revealed. Also notch stresses existing after an injury, get reduced through striving for a consistent tension at the surface.
Flexible Geometry Description
The shape of the component gets described by flexible splines which get controlled by the design variables. The splines can be described with lines and areas.

Fig. DLR Köln
Application Example:
Shape Optimization of a Tensile Test Specimen of Brittle Material
By optimizing the shape of transitional area, the probability of failure in this area should be minimized. Regarding such deterministicalle, the samples in the transitional area must actually fail due to the notch stresses. A desired failure in the measuring range is only possible with local faults. Possible pores in the material get therefore considered in the analysis model. The optimal shape depends on he pore density.
